Air Atlanta A306 at East Midlands on Jan 10th 2011, tailstrike on landing, go-around with open thrust reverser
Last Update: May 10, 2012 / 16:12:02 GMT/Zulu time
Incident Facts
Date of incident
Jan 10, 2011
Aircraft Registration
N852UA
Aircraft Type
Airbus A300
ICAO Type Designator
A306
This incident highlights the potentially serious consequences of attempting to go around after selection of reverse thrust. In this instance the failure of the No 2 thrust reverser to restow was most likely caused by a latent intermittent loose connection in the auto-restow circuit. However, even in the absence of this particular failure, the FCOM advises damage to the thrust reverser with equally significant consequences may still occur as a result of stow command being made while the reversers are in transit. The investigation identified a number of other anomalies with thrust reverser components, which may have contributed, either in isolation or combination, to the failure of the No 2 thrust reverser to restow.
This event also highlights the need for the operational procedures for use of thrust reversers and for performing a go-around to be unambiguous.
Furthermore, it illustrates the value of conducting annual downloads of CVRs in identifying dormant failures in these units, which have the potential to compromise the quality of safety investigations.
The captain (45, ATPL, 5,282 hours total, 4,600 hours on type) was pilot flying for the sector.
On approach to East Midlands the crew computed Vref at 135 KIAS and decided to use Vapp of 144 KIAS in response to the gusting nature of the winds reported by ATC at 20 knots from 160 degrees gusting up to 30 knots. There was light rain, the runway was wet.
The crew positioned the aircraft for an ILS runway 09 landing and configured the aircraft for a full flaps landing.
Descending through 1000 feet established on the ILS the commander requested a wind check, the wind was reported at 22 knots from 160 degrees. The captain later reported he began his flare as usual at 30 feet AGL and closed the throttle levers at 20 feet AGL, however considered the rate of descent excessive and therefore increased the pitch attitude. The aircraft touched down briefly with its main gear at 135 KCAS (138 knots above ground) and bounced, the squat switches did not indicate "on ground", the commander reduced the pitch slightly to allow the aircraft settle back onto the runway, the aircraft touched down heavily at +1.8G, the squat switches indicated "on ground" releasing spoilers and thrust reversers to deploy, and bounced again. Neither pilot recalled having selecting reverse thrust, however, the flight data recorder recorded the thrust reversers had been selected and had deployed but not reached their fully deployed position.
Following the second bounce the captain decided to go-around, selected full thrust on both throttle levers, full flaps and landing gear remained selected as the aircraft initiated the go-around, the pitch attitude increased from 5 degrees to 12.5 degrees nose up with the main gear still compressed (tailstrike possible at 11.2 degrees nose up with main gear compressed), the aircraft lifted off about 2 seconds later at 127 KIAS. The left engine accelerated to produce full thrust, the right engine remained at idle thrust. The aircraft climbed to 92 feet AGL within 13 seconds, the airspeed remained below Vref of 135 KIAS. Seven seconds after the main wheels departed the runway surface the flaps were reduced one step and another 5 seconds later the gear was retracted, the flight data recorder showed the left hand engine thrust reverser unlocked for a period of 16 seconds around the time, the engine however remained at full thrust. The aircraft levelled for a few seconds, accelerated to Vref and continued to climb taking 25 seconds for the next 100 feet of climb, the airspeed increased to 152 KIAS. The aircraft levelled again at 200 feet AGL for about 8 seconds, the airspeed increased to 160 KIAS and the aircraft subsequently climbed away with a significantly increased rate of climb.
About two minutes after the main wheels departed the runway surface after the second touch down the thrust lever for the right hand engine was reduced to idle, no further movements of the lever were recorded. 11 minutes after becoming airborne after the go-around the right hand engine was shut down.
The tower controller perceived the landing as firm, saw a shower of sparks coming from the rear of the aircraft, then the aircraft flew very slowly over the runway rolling from side to side and not climbing to more than 200 feet. He was sufficiently concerned to press the crash button but refrained from contacting the crew to not distract them. About 3nm east of the airfield the aircraft was seen climbing.
The commander later reported he had difficulty to accelerate the aircraft following the go-around. Eventually the speed increased and he instructed the first officer to reduce flaps to 20, and when the aircraft started to climb to retract the gear. When the aircraft climbed out and accelerated the flaps were retracted. At this point they noticed the right hand thrust reverser was indicated unlocked at their ECAM display. The captain retarded the throttle lever and operated the thrust reverser in an attempt to lock the thrust reverser however to no avail. The crew subsequently actioned the relevant checklist and shut the engine down.
After reviewing weather conditions the crew decided to divert to Stansted where the aircraft touched safely on runway 22. The commander selected reverse thrust on the left hand engine, the first officer reported the thrust reverser had not engaged properly so that the captain cancelled reverse thrust.
A subsequent examination of the aircraft at Stansted revealed the aircraft had suffered a tailstrike receiving damage to the tailskid shoe and a 3mm deep dent and scraping damage to the fuselage tail skin right of the tailskid shoe.
The AAIB analysed that the engines thrust reversers feature an auto-restow circuit which should ensure the thrust reverser sleeves are moved back into their stowed position automatically should the electrical power fail during the deploy cycle, the microswitches in the throttle quadrant remain energized from the time the stow sensors disengage (the sleeves are out of their stowed position) until the stow sensors register the sleeves are in their stowed position again. That way the auto-restow circuitry ensures the thrust reversers get closed again should they open in flight or should the thrust lever be moved into the stow position.
An engineer in Stansted noticed that the right hand engine's thrust reverser sleeve was open by about 25cm (10 inches), about half of the full the travel of 53cm. After opening the fan cowl doors he noticed the upper flexible drive shafts from the splitter gearbox to the master actuators on both sides were twisted and the secondary locks were not engaged. He hand cranked the sleeve into its stowed position, the flexible shafts disconnected at the master actuator ends to remove the tension and re-installed.
Subsequently engine runs were conducted during which both thrust reversers deployed and stowed correctly, the right hand engine however did not accelerate beyond idle thrust after the thrust reverser deployed indicating FADEC was limiting the engine thrust.
After several components were replaced the operator still experienced problems with the upper flexible drive shafts failing, the issue was determined to be a rigging issue following component removal and installation and were not considered relevant to the incident scenario.
During inspection of the auto-restow circuit wiring a loose cable was detected which would interrupt the electrical signal to the solenoid arming the auto-restow circuit. No trouble shooting manual was available to identify such a fault.
The AAIB analysed that the FCOM procedures requring a landing to be continued after thrust reversers were deployed and the bounced landing procedures contradicted each other. Airbus intends to update the FCOM bounced landing procedure to emphasize, that after thrust reverser deployment a full stop landing has to be completed.
The AAIB analysed that when the go-around was initiated at 127 KIAS and the aircraft became airborne at 127 KIAS, the airspeed was above Vmca however was significantly below the certified rotation speed of 144 KIAS required and thus resulted in reduced controls effectiveness. The higher angle of attack produced a higher aerodynamic drag further compromising the aircraft's acceleration and climb performance.
Recordings of the flight data recorder showed that the thrust reversers were selected open, the thrust reverser sleeves however had not sufficient time to reach their fully deployed positions before the thrust levers were pushed forward for the go-around. The FCOM states that during the sleeve transition the throttle levers must not be psuhed towards the stowed position as this may cause damage to the system like twisting or binding.
The AAIB analysed: "The most significant finding was the identification of a loose wire in the auto-restow circuit, which is designed not only to ensure the stowing of the thrust reversers during normal operation, but also in the case of an in‑flight thrust reverser deployment. Loss of electrical signal to the PRSOV arming solenoid following the mid-stroke stow command, as a result of the loose wire, is considered the most likely reason for the No 2 thrust reverser stopping in the mid-stroke position. The loose connection is considered to have been an intermittent issue; had this been a permanent condition, the normal stowing function of the thrust reversers would have been compromised prior to the incident and this would also have been evident during the post-incident function checks and engine runs and following the aircraftÂ’s return to service."
Incident Facts
Date of incident
Jan 10, 2011
Aircraft Registration
N852UA
Aircraft Type
Airbus A300
ICAO Type Designator
A306
This article is published under license from Avherald.com. © of text by Avherald.com.
Article source
You can read 2 more free articles without a subscription.
Subscribe now and continue reading without any limits!
Read unlimited articles and receive our daily update briefing. Gain better insights into what is happening in commercial aviation safety.
Send tip
Support AeroInside by sending a small tip amount.
Related articles
United A319 at Austin on Feb 6th 2023, hydraulic failure
A United Airbus A319-100, registration N852UA performing flight UA-1784 from Houston Intercontinental,TX to Austin,TX (USA), was descending towards…
Thomson B763 at Bristol on Oct 3rd 2010, hard landing
The AAIB released their bulletin concluding the probable cause of the accident was:Damage to the fuselage occurred as a result of rapid…
United A319 near Denver on May 9th 2012, engine vibrations
A United Airlines Airbus A319-100, registration N852UA performing flight UA-867 from Toronto,ON (Canada) to San Francisco,CA (USA), was enroute at…
Newest articles
Dana MD82 at Lagos on Apr 23rd 2024, runway excursion
A Dana Air McDonnell Douglas MD-82, registration 5N-BKI performing flight 9J-352 from Abuja to Lagos (Nigeria) with 83 passengers and 6 crew, landed…
LATAM Brasil A320 at Brasilia on May 13th 2024, engine shut down in flight
A LATAM Brasil Airbus A320-200, registration PR-MYI performing flight LA-3008 from Sao Paulo Congonhas,SP to Brasilia,DF (Brazil) with 106 people on…
Subscribe today
Are you researching aviation incidents? Get access to AeroInside Insights, unlimited read access and receive the daily newsletter.
Pick your plan and subscribePartner

A new way to document and demonstrate airworthiness compliance and aircraft value. Find out more.
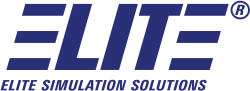
ELITE Simulation Solutions is a leading global provider of Flight Simulation Training Devices, IFR training software as well as flight controls and related services. Find out more.

Your regulation partner, specialists in aviation safety and compliance; providing training, auditing, and consultancy services. Find out more.
AeroInside Blog
Popular aircraft
Airbus A320Boeing 737-800
Boeing 737-800 MAX
Popular airlines
American AirlinesUnited
Delta
Air Canada
Lufthansa
British Airways